Newer
Older
1
2
3
4
5
6
7
8
9
10
11
12
13
14
15
16
17
18
19
20
21
22
23
24
25
26
27
28
29
30
31
32
33
34
35
36
37
38
39
40
41
42
43
44
45
46
47
48
49
50
51
52
53
54
55
56
57
58
59
60
61
62
63
64
65
66
67
68
69
70
71
72
73
74
75
Electronics production
======================
This week I made an in-circuit programmer- the FabISP.
FabISP
------
### Making toolpaths
I downloaded the png files for the traces and the interior. I used [FabModules](http://fabmodules.org/) to create toolpaths.
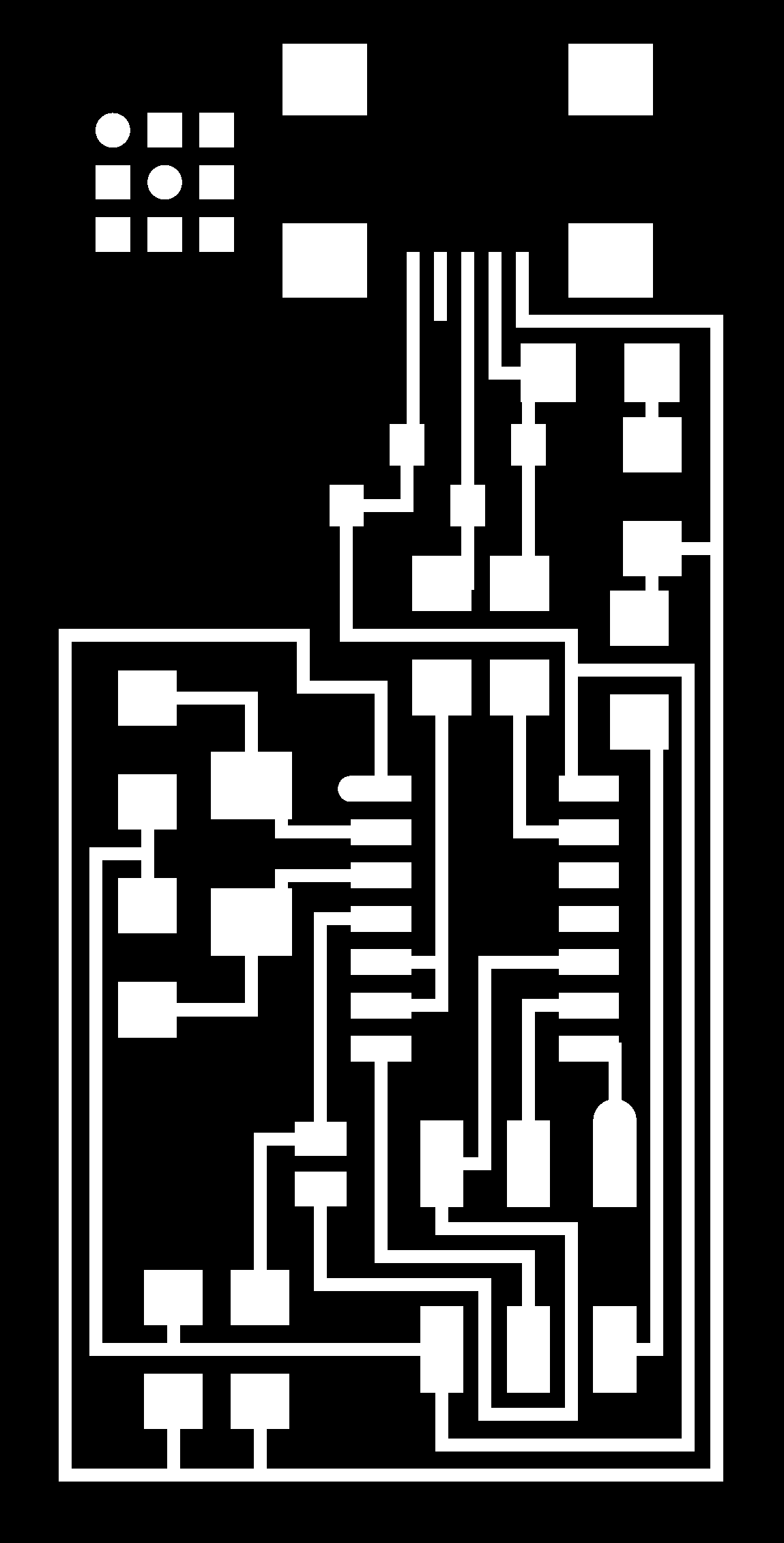
#### Traces
The major settings for cutting traces: Input image as **.png**
Output file as **.rml**
Output file as **.rml**
Machine: **Roland SRM-20**
Speed: **3.5mm/s** as I was using a new endmill
Origin X,Y,Z as **0,0,0** to match the origin set in the machine locally Tool diameter **1/64"** Offset paths **4**, to clean area around the traces but not very time consuming Overlap **50%**, overlaping the tool paths by 50% of the tool diameter Cut depth **0.1mm** to clean the top copper layer thorugh it's thickness

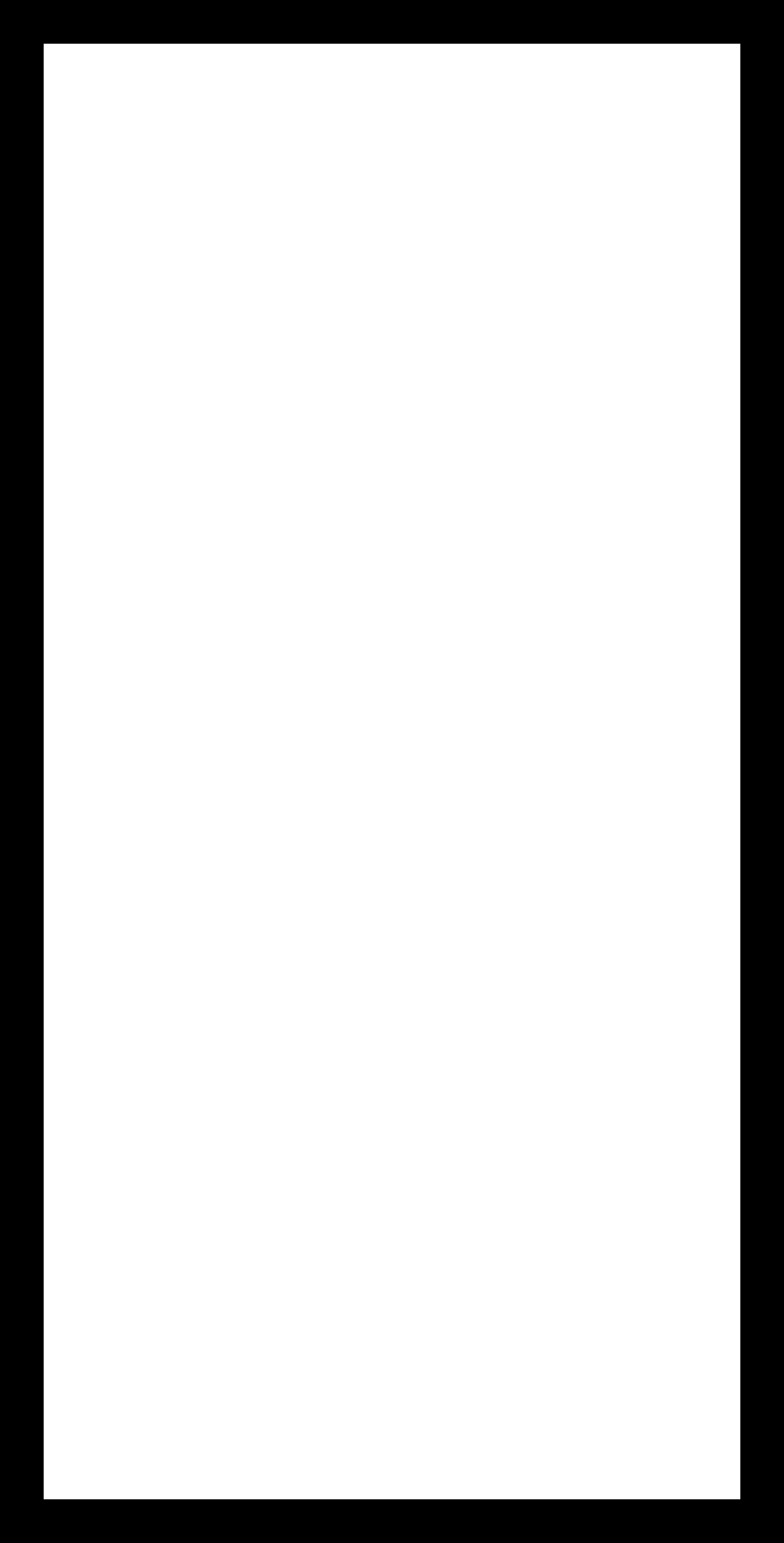
#### Interior
Settings for cutting the outline: Input image as **.png**
Output file as **.rml**
Machine: Roland **SRM-20**
Speed: **0.5mm/s** Material depth **1.7mm**, equal to the one-sided FR1 board used Cut depth **0.5mm**, cuts the outline 4 times going 0.5mm deeper with every loop Origin X,Y,Z as **0,0,0** to match the origin set in the machine locally and match the traces file Tool diameter **1/32"** Offset paths **1**, to cut the board from the material
### Milling the board
Cleaned a small piece of one-sided FR1 board with rubbing alcohol Stuck it using a double-sided tape on an MDF base we have pre-installed at the lab, that is levelled periodically. Installed a 1/64" tool Set the X and Y origin on the bottom left corner of the board. Brought the Z really close to the top of the surfect. Loosened the collet and let the bit touch the surface completely. Set the Z origin here. Lifted the Z, loaded the rml traces file and start cutting. Evrything seemed fine. I could see the tool cut though the copper. It took about 15 minutes to cut the whole file. Later, I lifted the Z, changed the tool to the 1/32" endmill to cut the interior file. I set the Z origin again exactly as before. Keeping in mind not to change the X and Y origin. Started cutting the file. Got it done on the first try. I unattached the board using a scraper.  
### Soldering Components
#### Gathering Components
Edu showed us the best way to do this was to make a shopping list, collect components and stick them on using tape. Later, we update the inventory sheet to keep count in the lab.
A list of all the needed components:
1 x ATtiny44 (Ict44)
1 x 6-pin(2x3) header (J1 ISP)
1 x MiniUSB header (J2 USB)
1 x 20MHz Crystal (20MHz)
1 x 1uF Capacitor (C1)
2 x 10pF Capacitor (C2,C3)
2 x 3.3v Zener Diodes (D1,D2)
1 x 1kΩ Resistor (R1)
1 x 499Ω resistor (R2)
1 x 100Ω resistor (R3,R4)
1 x 10kΩ resistor (R5)
2 x 0Ω Resistor (SJ1, SJ2)

#### The solding set-up
Tools that I need to solder the components on the board: A schematic diagram that shows what components goes where.
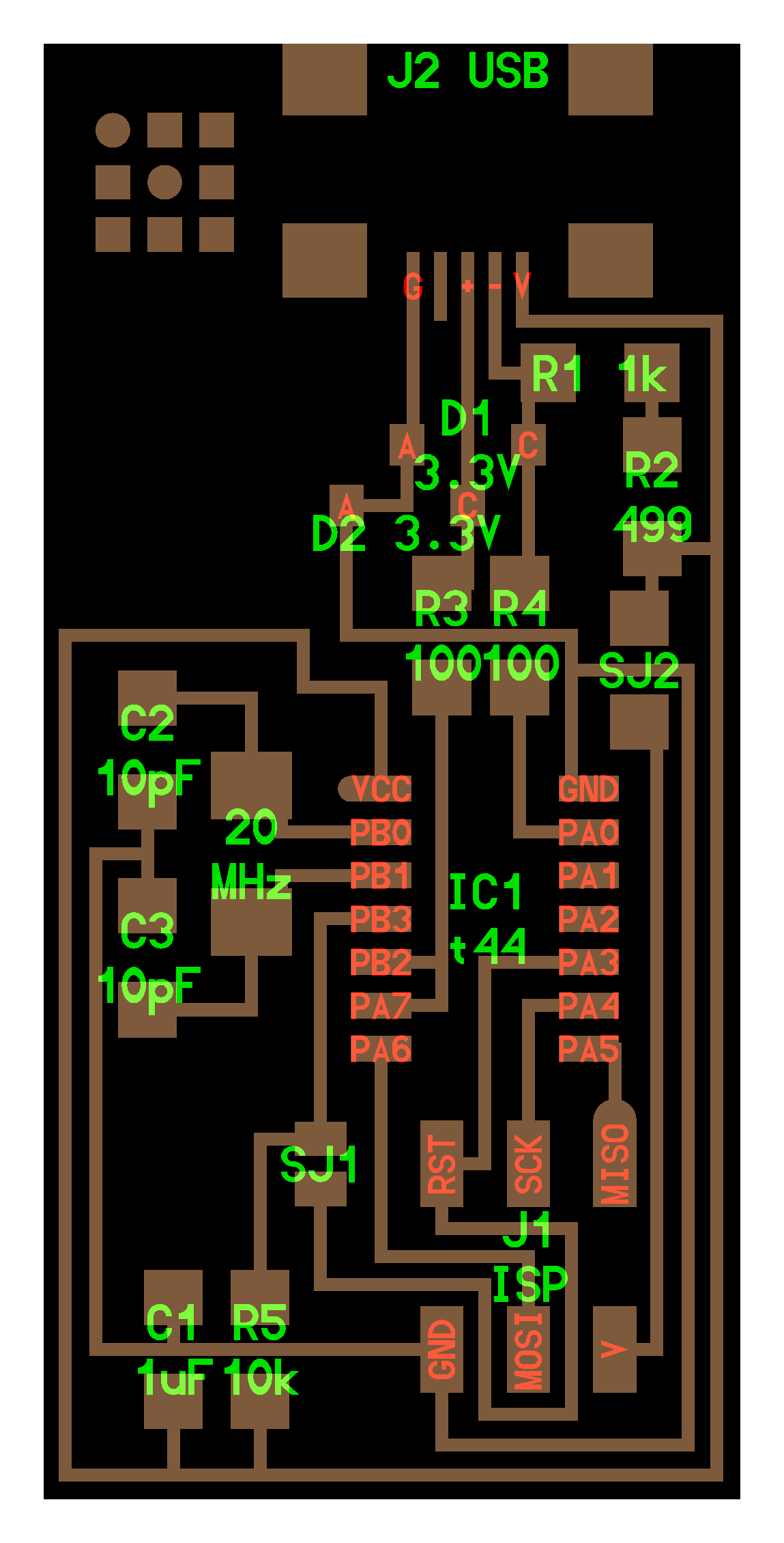
The components, gathered on the list. A soldering iron - I used a Weller WES51 with temperature control. Set it to 750F, not too hot, not too slow. A wet sponge, to clean the tip of the iron. Solder wire, Kester without a flux co. A anti-static curved tweezer to place down components accurately. A copper braid for desoldering excess solder. A table-top light, a silicon base to hold the board stationary, and a fan to remove fumes.
#### Soldering order
I started from the complex to the simple, then top to bottom. I soldered the microcontroller first, matched the orientation from from the data sheet. Second, I soldered the MiniUSB, since, it had very tiny trace connections. The zener diodes, have polarities. i soldered them next. Oscar taught me how the way to remember their direction, the electric symbol has a line that corresponds to the Cathode. Similarly, the component is marked with a line in its cathode side. Polarity symbol The rest of the components don't have any polarities, so I soldered them from top to bottom inside-out in this order: R1>R2>R3>R4>SJ2>20MHz>C2>C3>SJ1>R5>C1 and the J1 header in the end, because it had comparatively larger feet
#### Checking connections
I visually checked the board under a lens to check no traces or solders touched each other. Then using a multimeter setting with no resistance, I connected all pin legs to where the traces connected using the schematic diagram. And checked that all beeped, suggesting there was no short. I cleaned the board again, using some rubbing alcohol. This is how my finished board looks: 
#### Testing the board
[steps](http://archive.fabacademy.org/archives/2017/fablabverket/students/100/web/assignments/week4/index.html#programming) [or these](http://archive.fabacademy.org/archives/2017/fablabverket/students/100/web/assignments/week4/index.html#programming)