added bacterial dye
Showing
- docs/assignments/week04.md 8 additions, 8 deletionsdocs/assignments/week04.md
- docs/files/ingredients/linseedoil.md 2 additions, 1 deletiondocs/files/ingredients/linseedoil.md
- docs/files/recipes/bacterialdye.md 176 additions, 124 deletionsdocs/files/recipes/bacterialdye.md
- docs/files/recipes/cabbagedye.md 2 additions, 1 deletiondocs/files/recipes/cabbagedye.md
- docs/files/recipes/fishskin.md 1 addition, 1 deletiondocs/files/recipes/fishskin.md
- docs/files/recipes/kombuchapaper.md 1 addition, 1 deletiondocs/files/recipes/kombuchapaper.md
- docs/files/recipes/madderdye.md 15 additions, 6 deletionsdocs/files/recipes/madderdye.md
- docs/files/recipes/phmodifiers.md 103 additions, 137 deletionsdocs/files/recipes/phmodifiers.md
- docs/images/bacteria1.jpg 0 additions, 0 deletionsdocs/images/bacteria1.jpg
- docs/images/bacteria10.jpg 0 additions, 0 deletionsdocs/images/bacteria10.jpg
- docs/images/bacteria2.jpg 0 additions, 0 deletionsdocs/images/bacteria2.jpg
- docs/images/bacteria3.jpg 0 additions, 0 deletionsdocs/images/bacteria3.jpg
- docs/images/bacteria4.jpg 0 additions, 0 deletionsdocs/images/bacteria4.jpg
- docs/images/bacteria5.jpg 0 additions, 0 deletionsdocs/images/bacteria5.jpg
- docs/images/bacteria6.jpg 0 additions, 0 deletionsdocs/images/bacteria6.jpg
- docs/images/bacteria7.jpg 0 additions, 0 deletionsdocs/images/bacteria7.jpg
- docs/images/bacteria8.jpg 0 additions, 0 deletionsdocs/images/bacteria8.jpg
- docs/images/bacteria9.jpg 0 additions, 0 deletionsdocs/images/bacteria9.jpg
- docs/images/finalpics-123.jpg 0 additions, 0 deletionsdocs/images/finalpics-123.jpg
- docs/images/finalpics-124.jpg 0 additions, 0 deletionsdocs/images/finalpics-124.jpg
This diff is collapsed.
docs/images/bacteria1.jpg
0 → 100644
126 KiB
docs/images/bacteria10.jpg
0 → 100644
146 KiB
docs/images/bacteria2.jpg
0 → 100644
98.1 KiB
docs/images/bacteria3.jpg
0 → 100644
154 KiB
docs/images/bacteria4.jpg
0 → 100644
123 KiB
docs/images/bacteria5.jpg
0 → 100644
176 KiB
docs/images/bacteria6.jpg
0 → 100644
164 KiB
docs/images/bacteria7.jpg
0 → 100644
109 KiB
docs/images/bacteria8.jpg
0 → 100644
143 KiB
docs/images/bacteria9.jpg
0 → 100644
168 KiB
docs/images/finalpics-123.jpg
0 → 100644
76.4 KiB
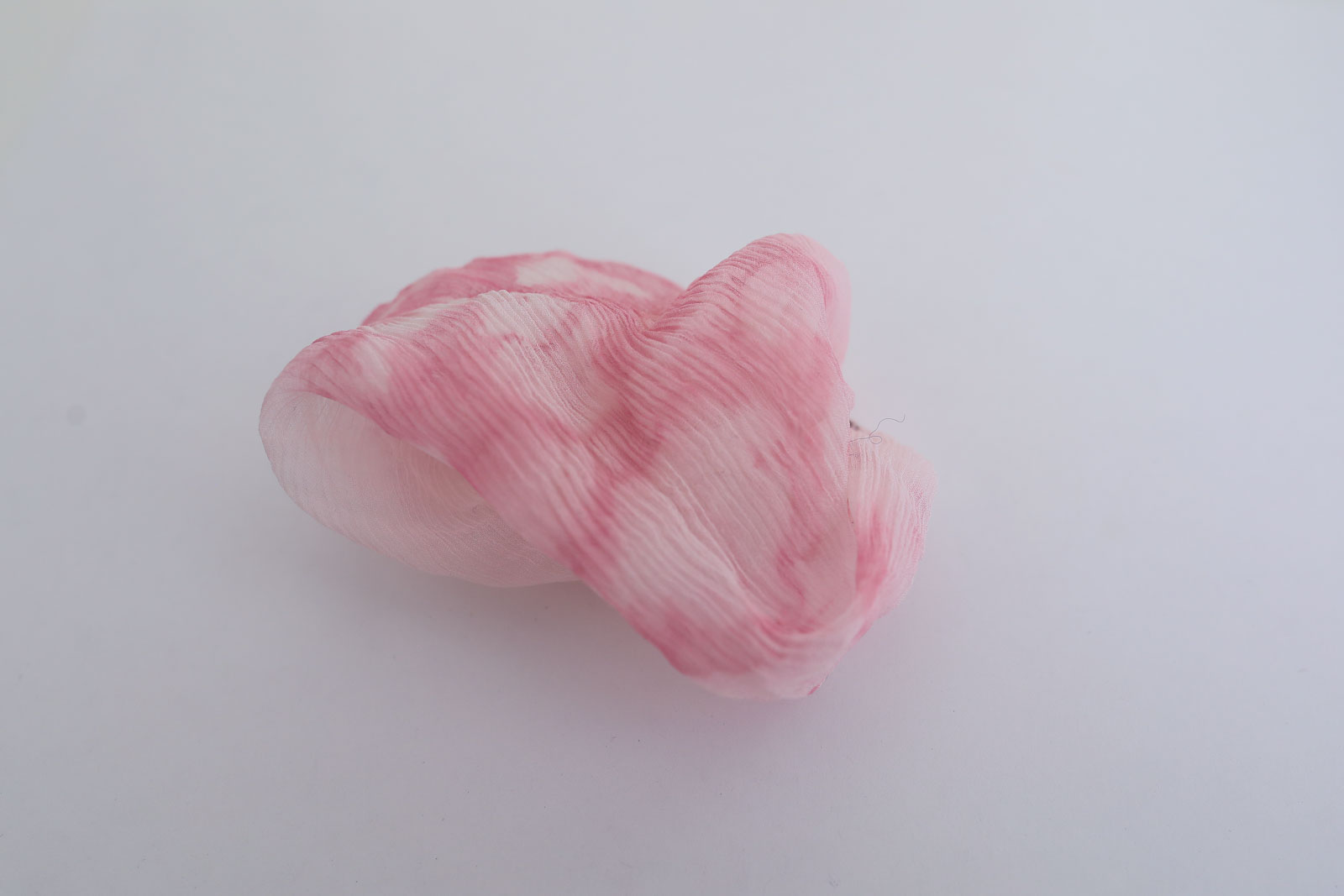
| W: | H:
| W: | H:
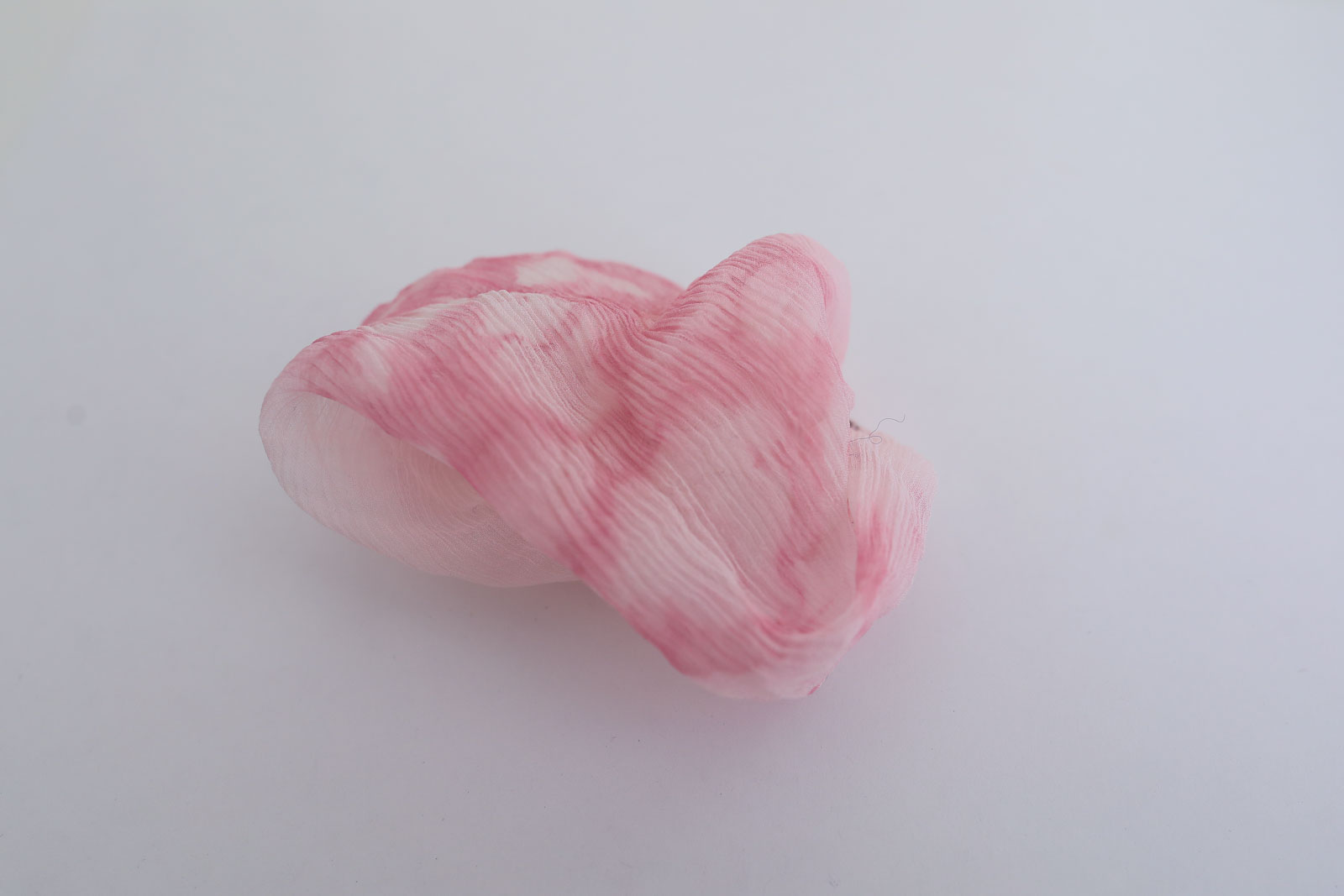
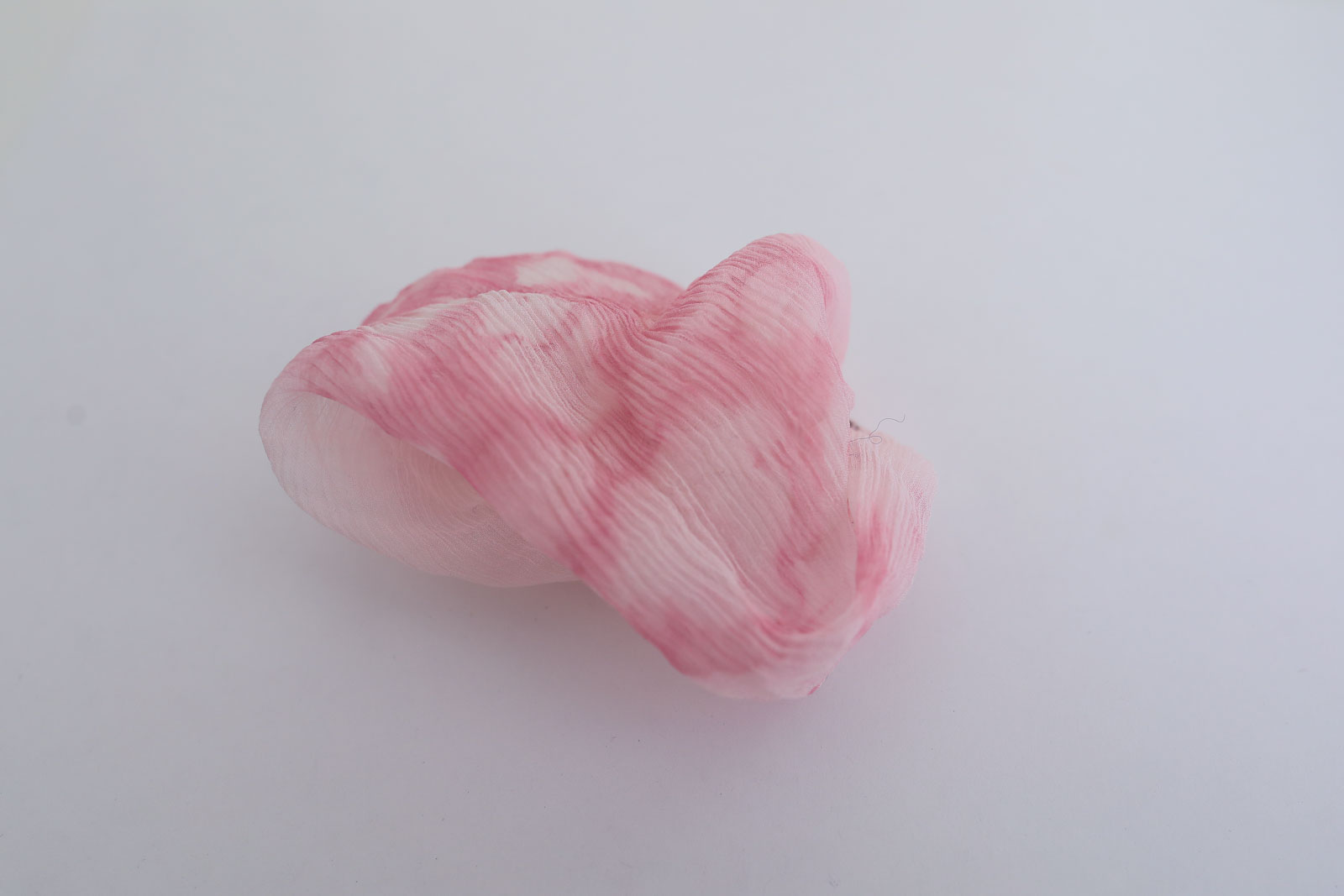