# 8. Computer controlled machining This week I worked on defining my final project idea and started to getting used to the documentation process. group assignment do your lab's safety training test runout, alignment, fixturing, speeds, feeds, materials, and toolpaths for your machine **Individual assignment** Make (design+mill+assemble) something big (~meter-scale) Extra credit: don't use fasteners or glue Extra credit: include curved surfaces ## Table design I used the following picture as a basic inspiration for my table 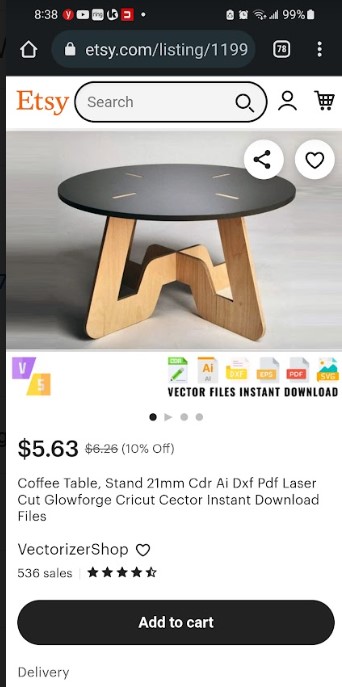 Hight: I started by looking up hight for table and is seems that card and dinning tables are typically 28-32 inches high. Work table are 28-30 inches and so I decided to go with 30 inches able top size: I decided to go with the biggest I can make which is going to be 48 inches Floor base: I found on line that the “golden rule” is to have the width of the base at the floor be at least 0.6x the overall height of the table. As this is the minimum I wanted to have a very stable table and decided to use 0.75 as the ratio. Table leg width: I will use 6 inches I plan to make this with a glue up of 3/4 inch hardwood planks (see next section) First up a set up a few parameters I plan to use based on the design approach I listed above 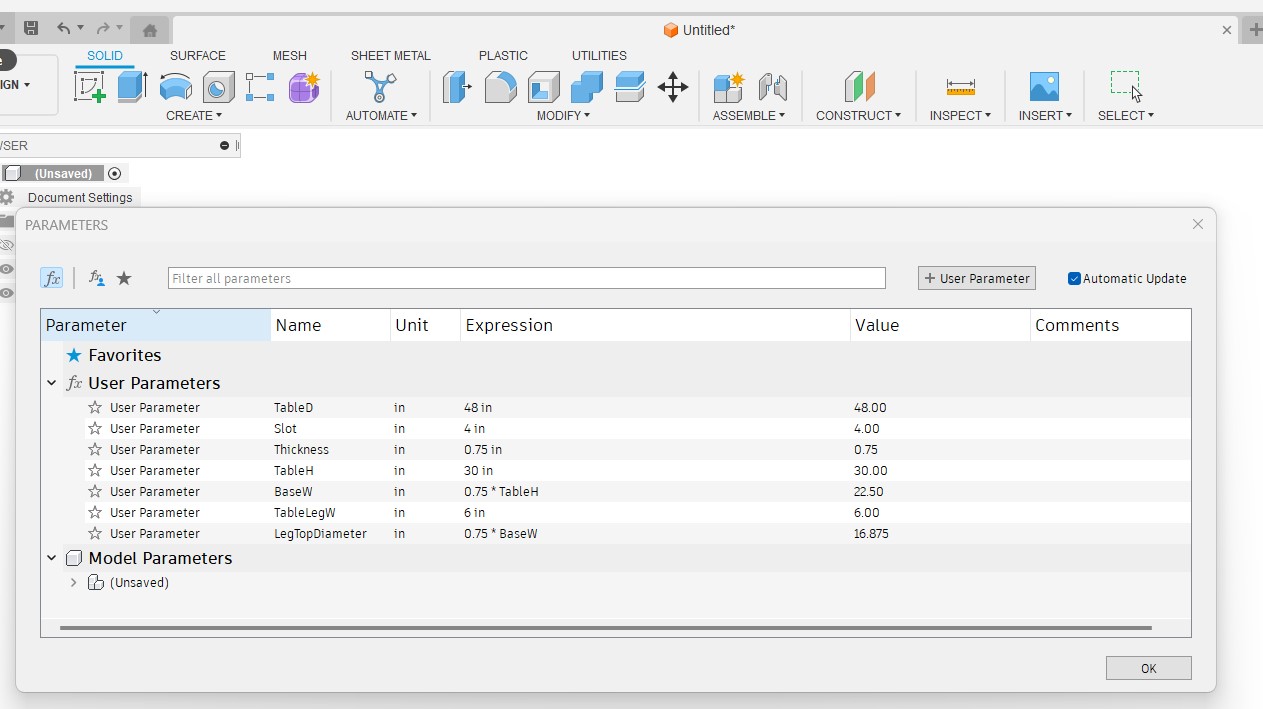 Next I started with the table top and slots 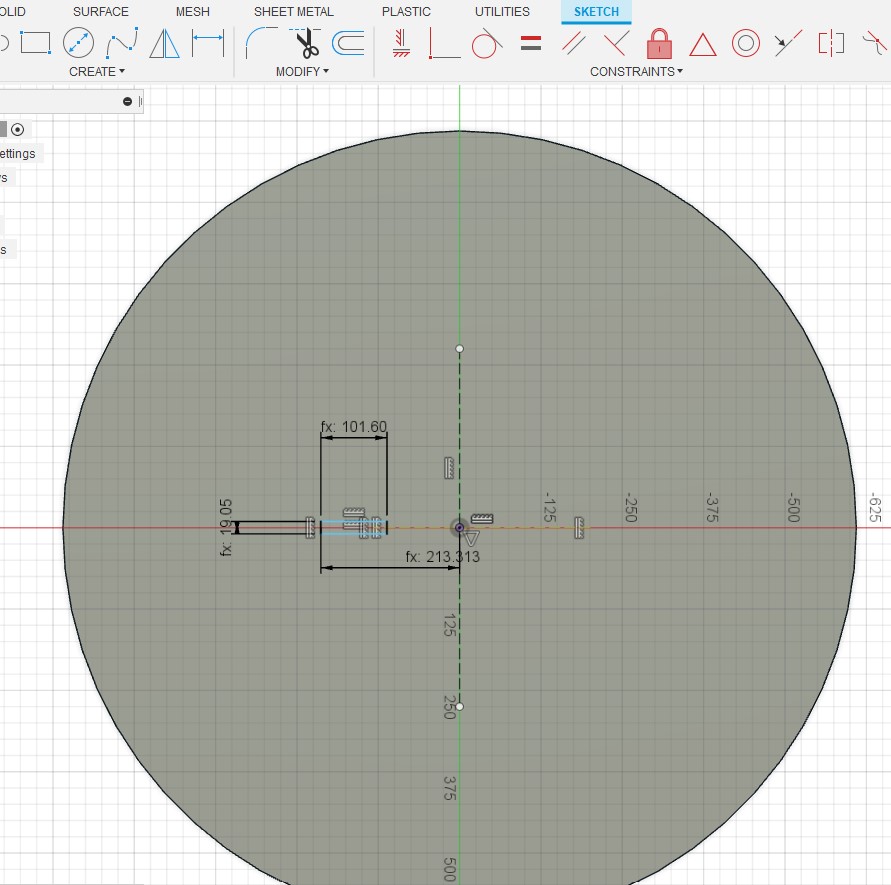 Circular patter repeat make this a quick one 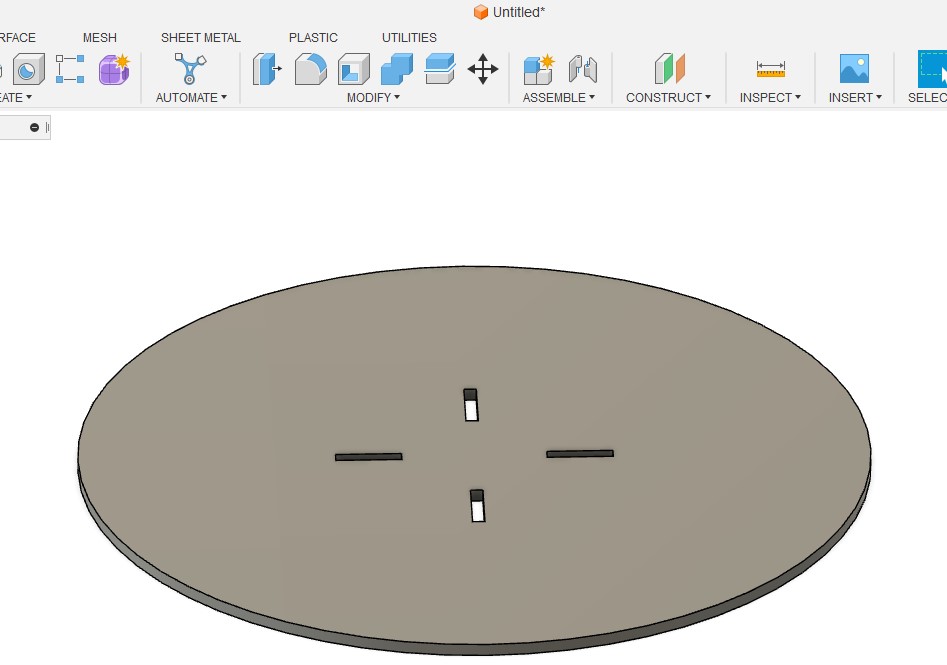 Next I started on the legs and was wanted to ensure the end of the leg can slide into the the slot in the table top 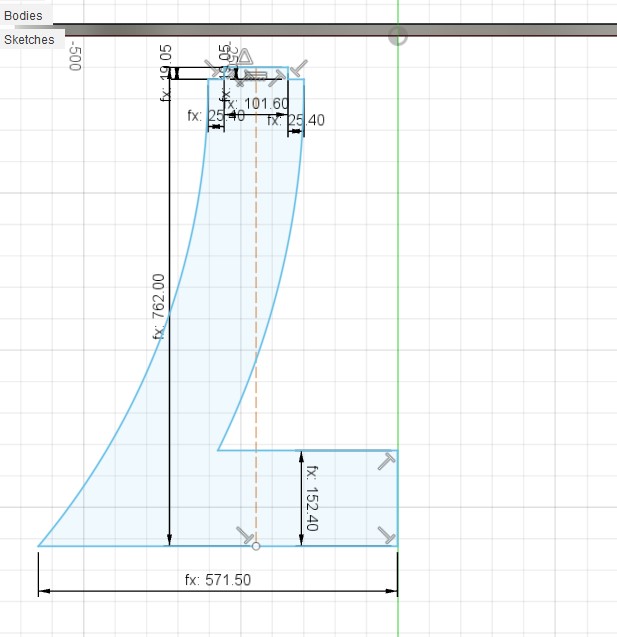 I set up the basic shape and mirrored in the sketch to ensure the legs were symmetrical - this was my first mistake as a later found out that mirroring in the sketch does not work as well a mirroring the extruded part when changing the user defined parameters 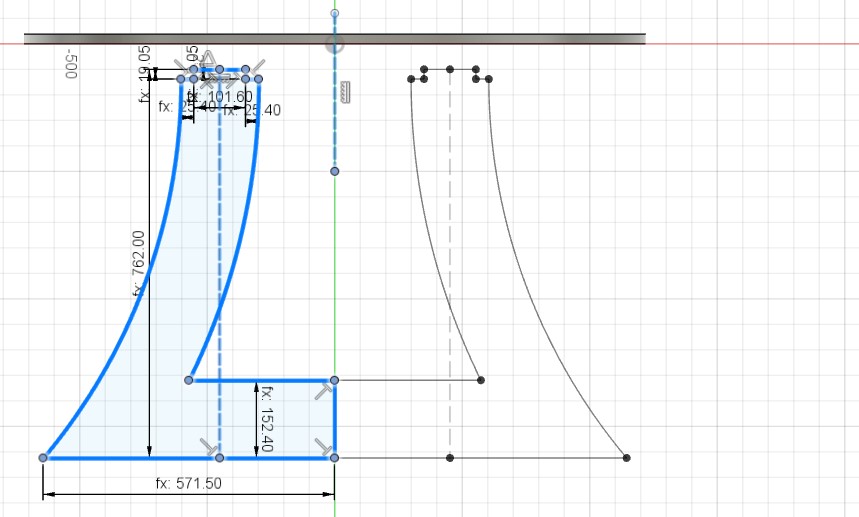 I got the legs ready with the cross fit joint 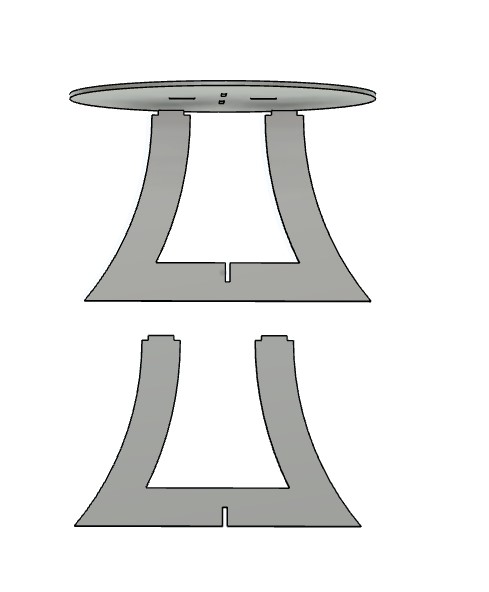 Next I decided to check fit in fusion and good thing I did as I has the slots misaligned 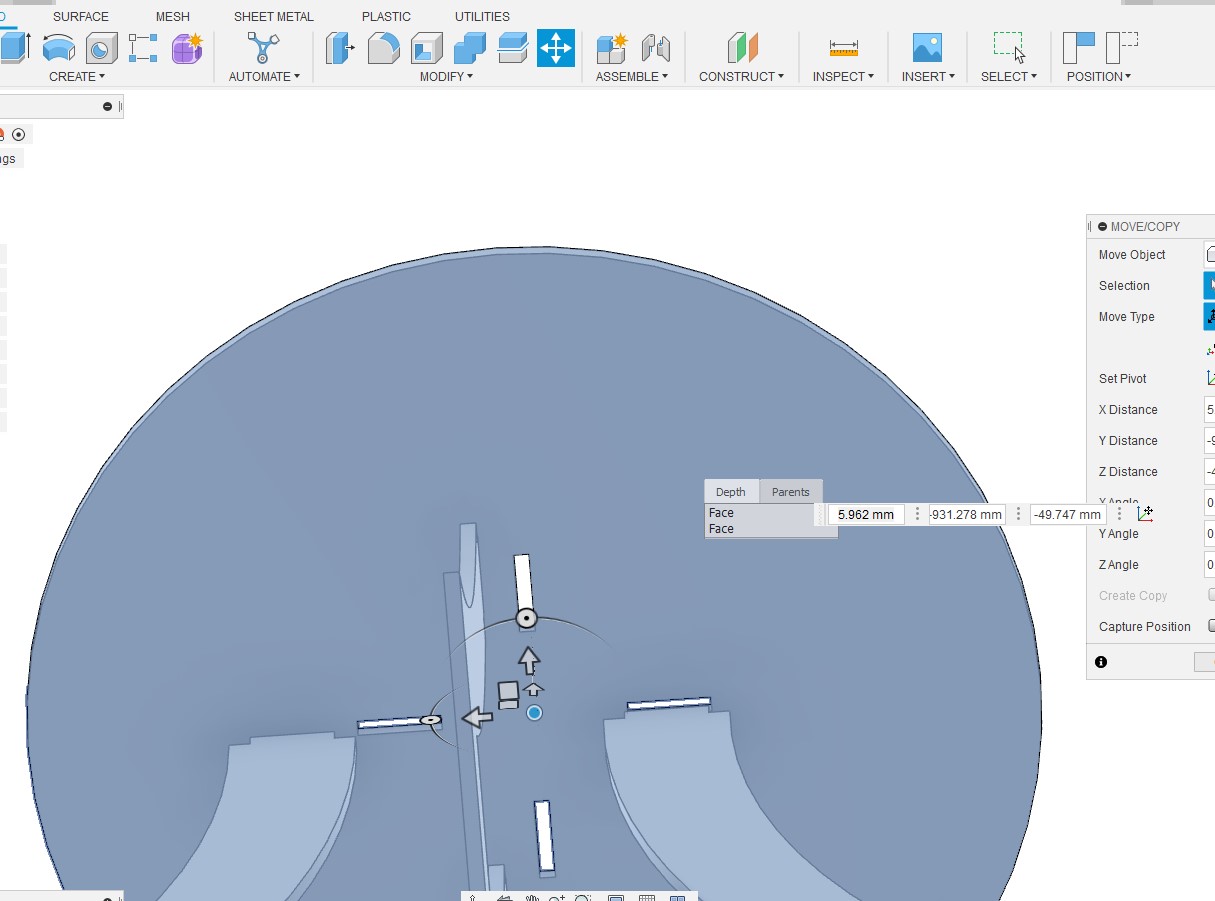 This called for a new parameter and I used sketch dimensions restriction to ensure they will line up 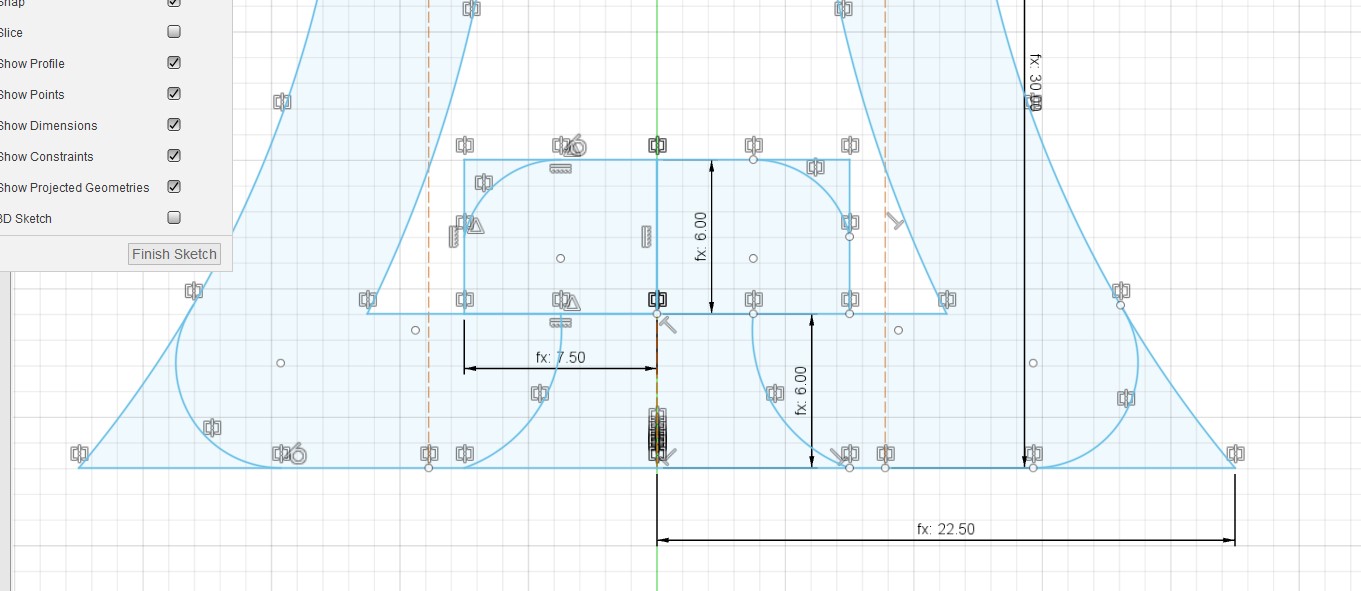 I used the same parameter in the top and leg to ensure alignment 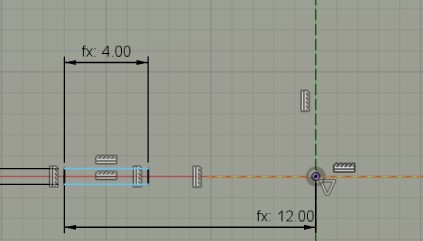 and another check - we are good to go  Now that we get that working I decided I really did not like the look of the legs and so it was time for design #2 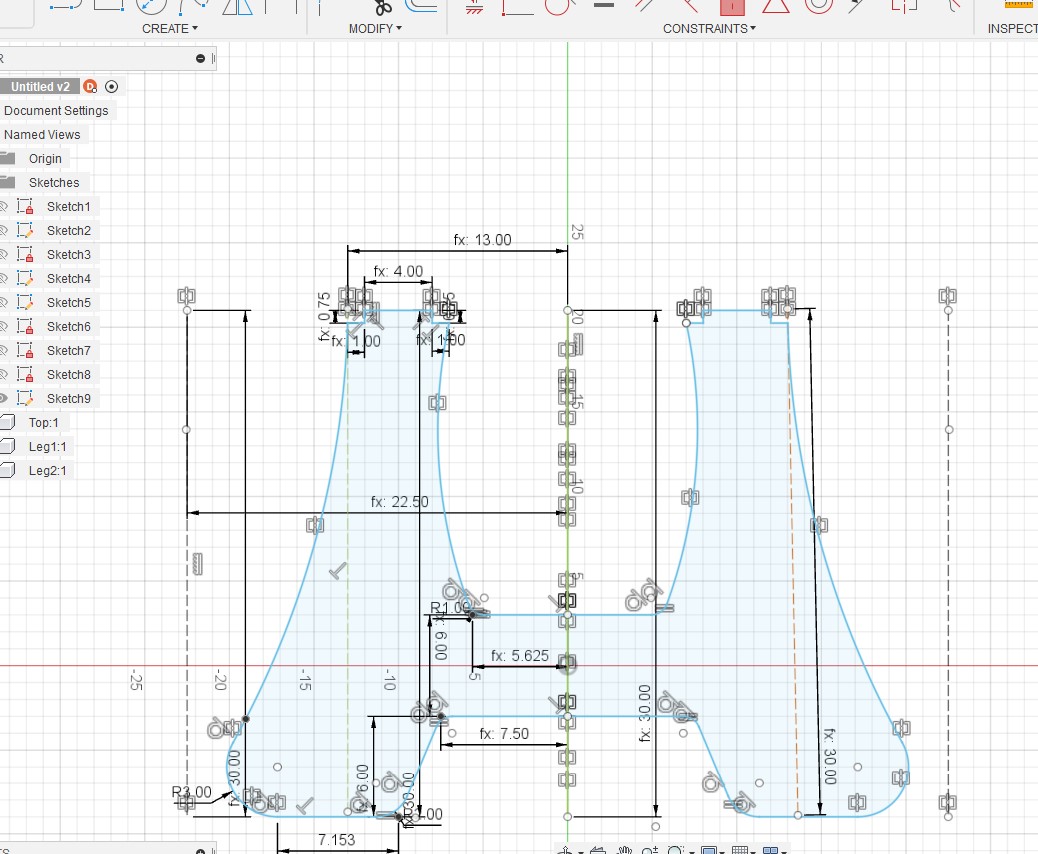 I repeated the steps above and had the next set of legs ready 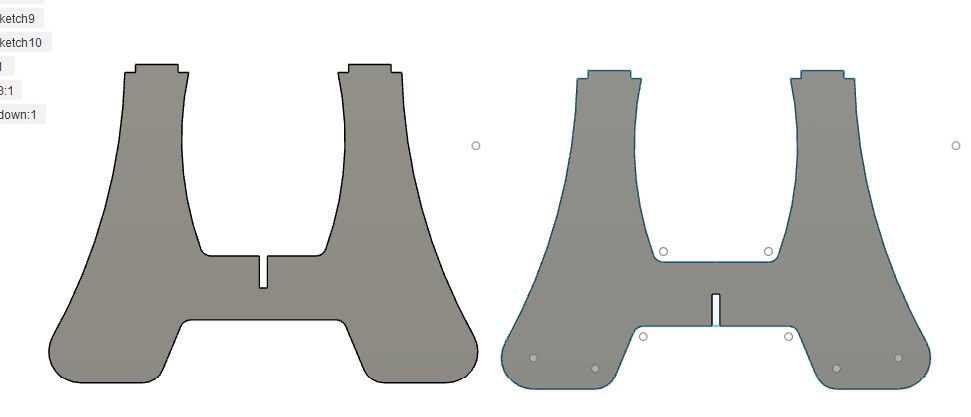 When I wanted to resize the legs the sketch profile kept coming apart and so after some research I decided to redo this once again the this time to use the 3d mirroring instead of the sketch. So here we go again 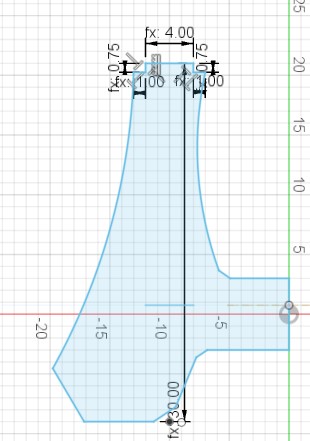 I extruded on this part 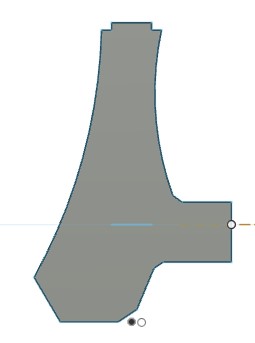 then mirrored it in 3D  duplicated and added joint 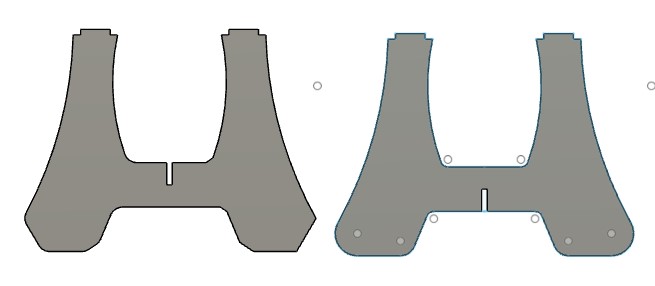 I downloaded a [Dogbone add-in](https://apps.autodesk.com/FUSION/en/Detail/Index?id=3534533763590670806&appLang=en&os=Win64) for Fusion and got the design ready to cut 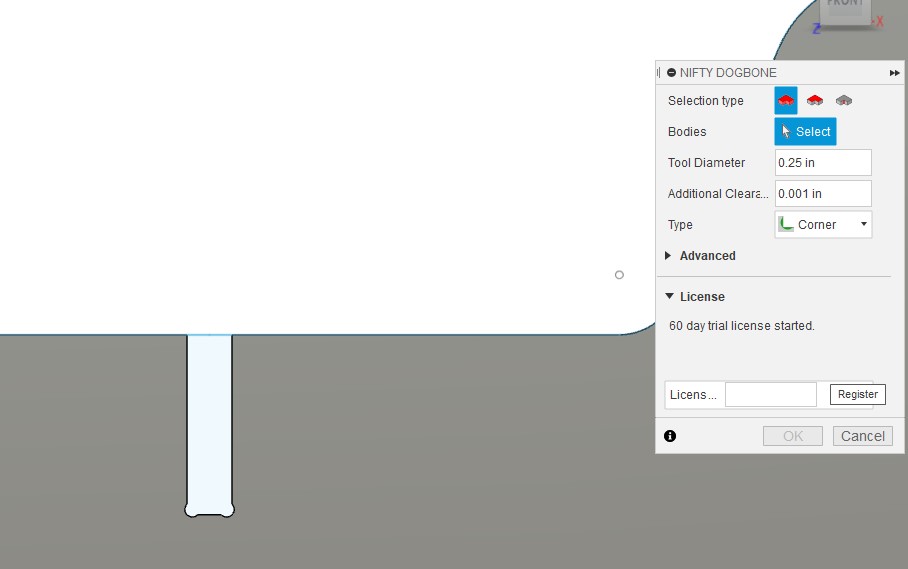 and now we are ready to mock up in the laser cutter 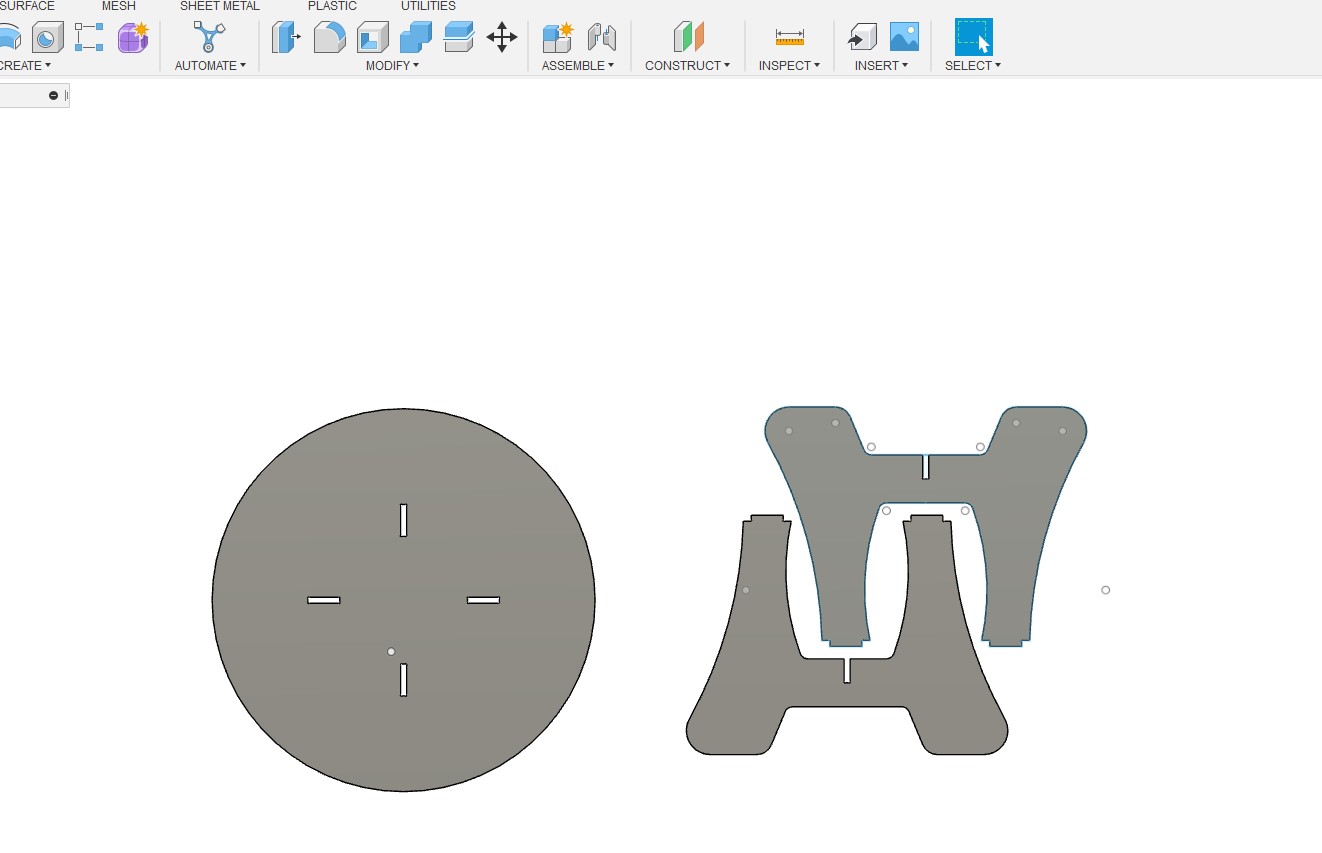 ## Laser cut mock up Next I took the basic table design and laser cut a small version to get a feel for fit and look 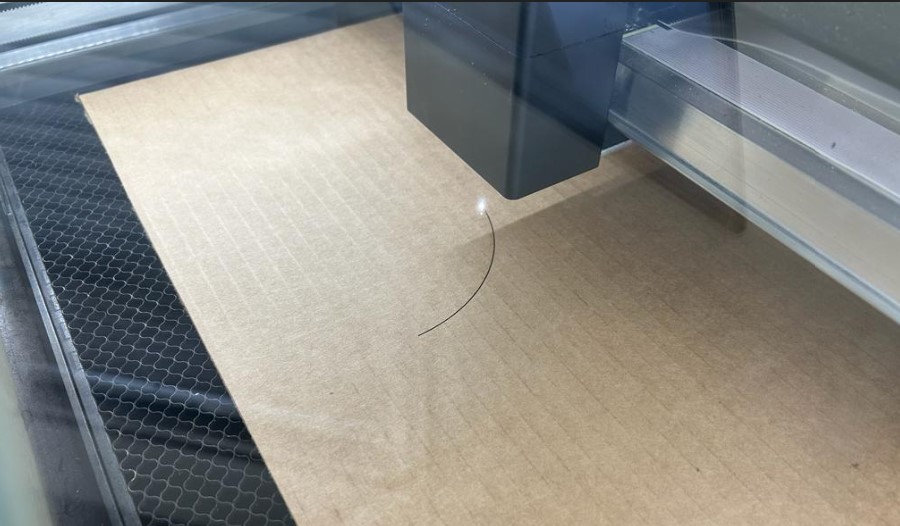 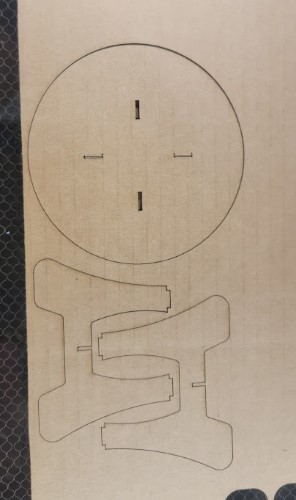 The table looked nice and legs seem to align well to the table top slots 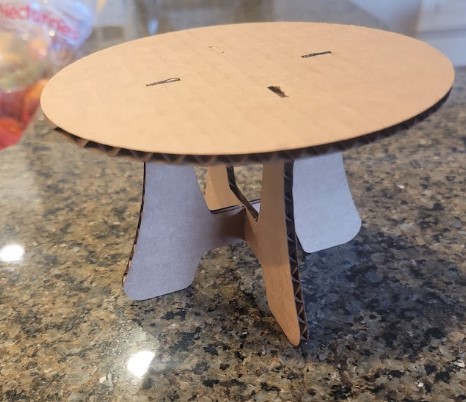 When I showed it to my kids they started playing with it and turn the legs upside down. This looked much better!!! 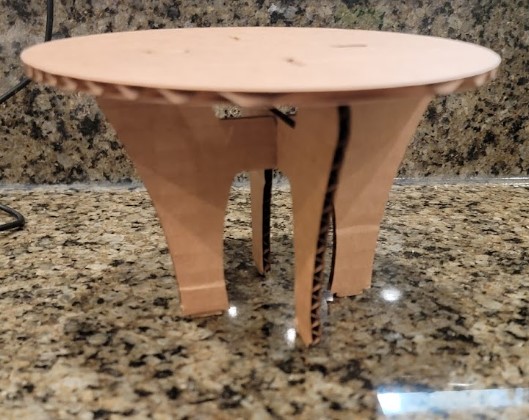 Now I needed to get back to fusion and redesign the legs. ## Leg design #2 To ensure i keep the slot in place I created a plan on the bottom and projected the slot on it 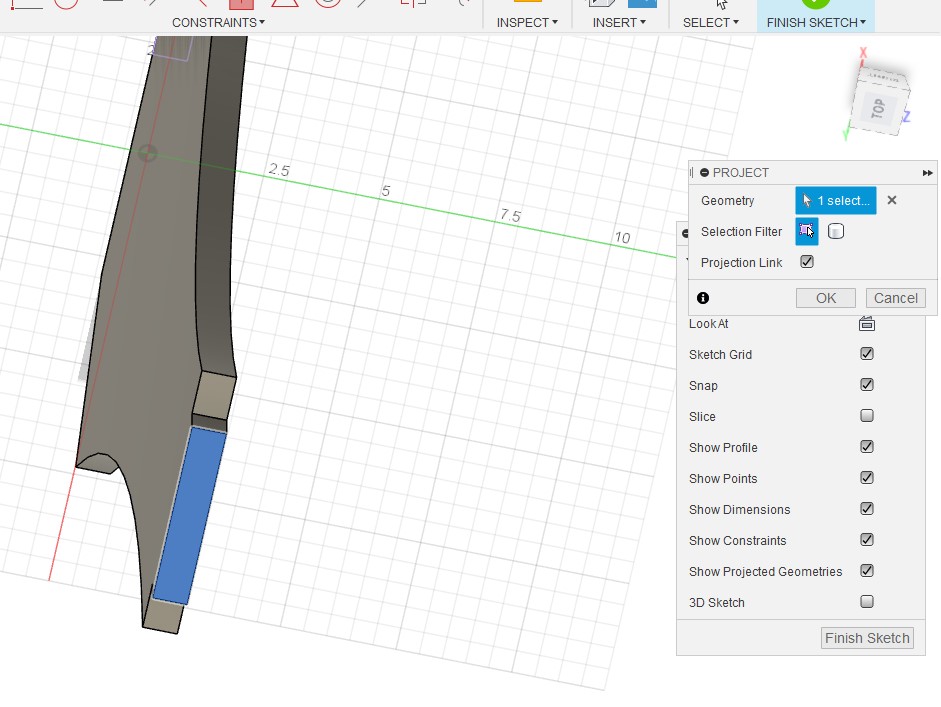 Then I saw that the leg was too narrow in that part 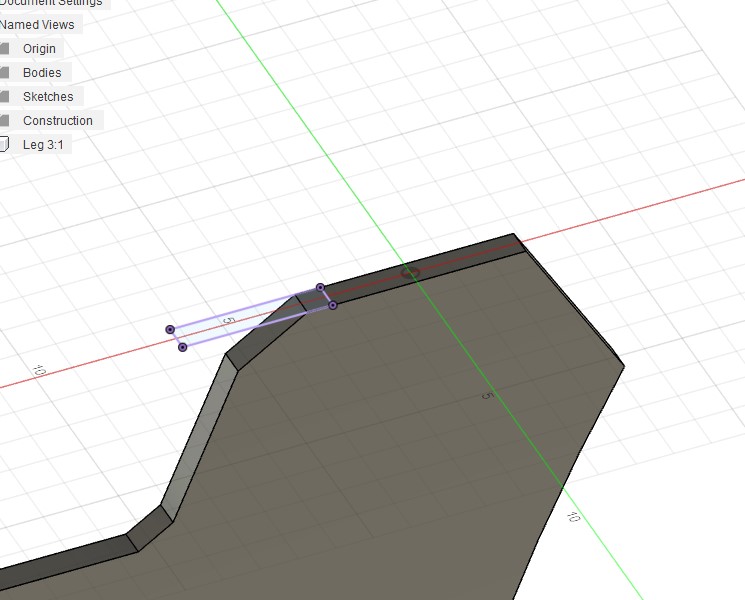 I extruded it but need to get the base back in line 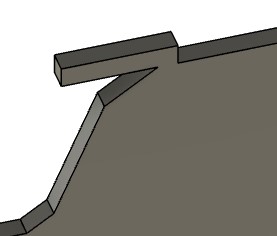 So a went back to the sketch and adjusted it 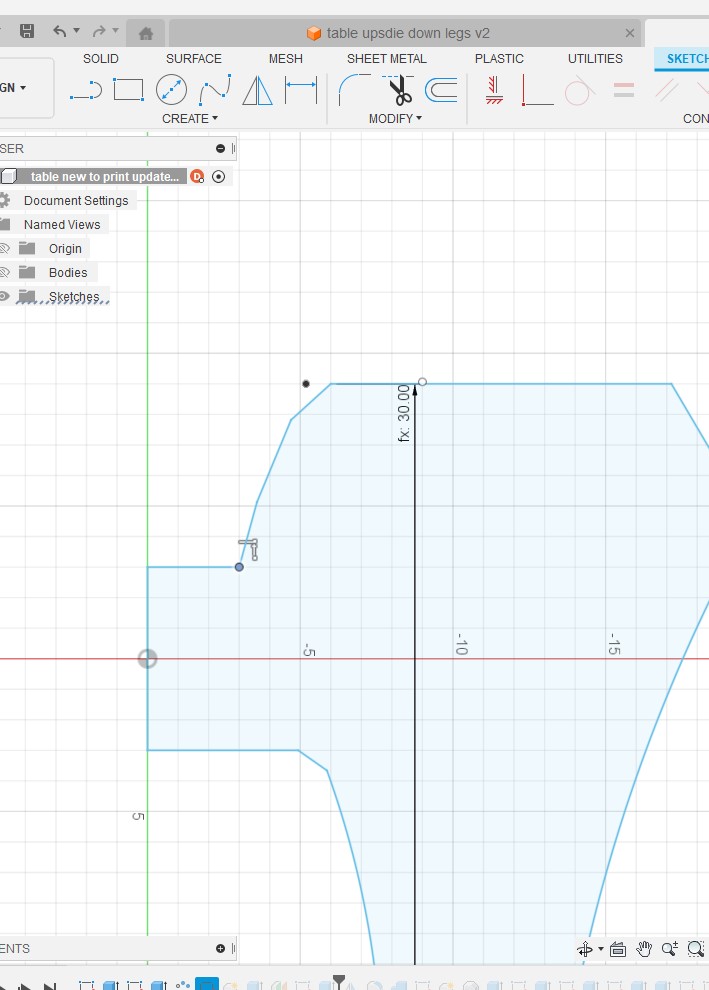 That looked good 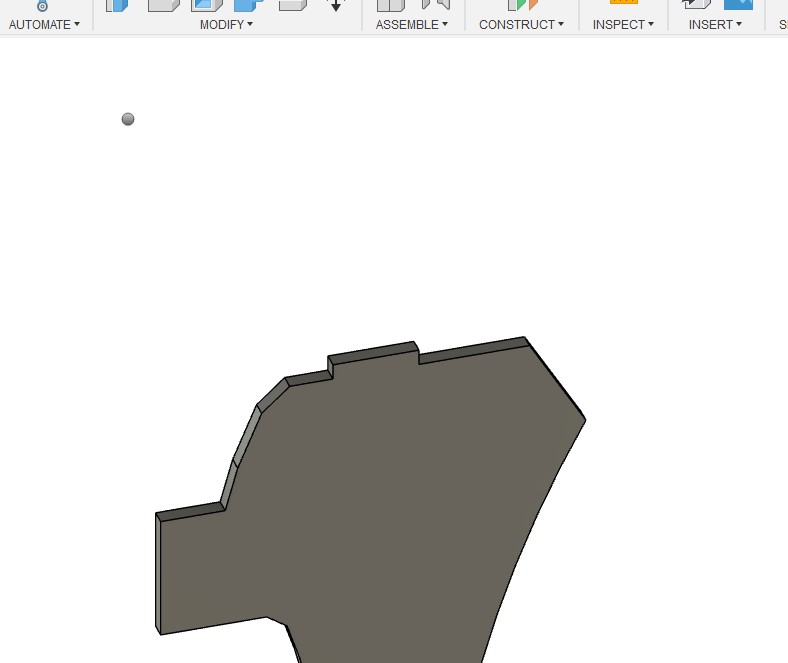 Now I needed to erase the old slot 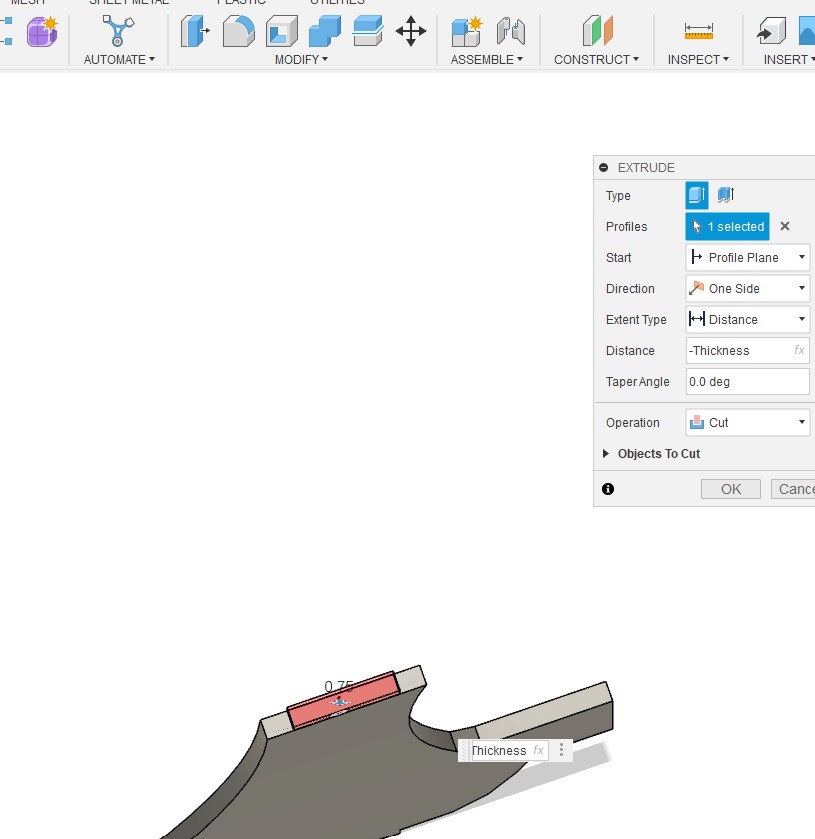 and this looks 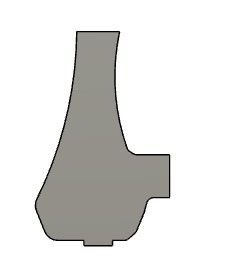 And we are good to go 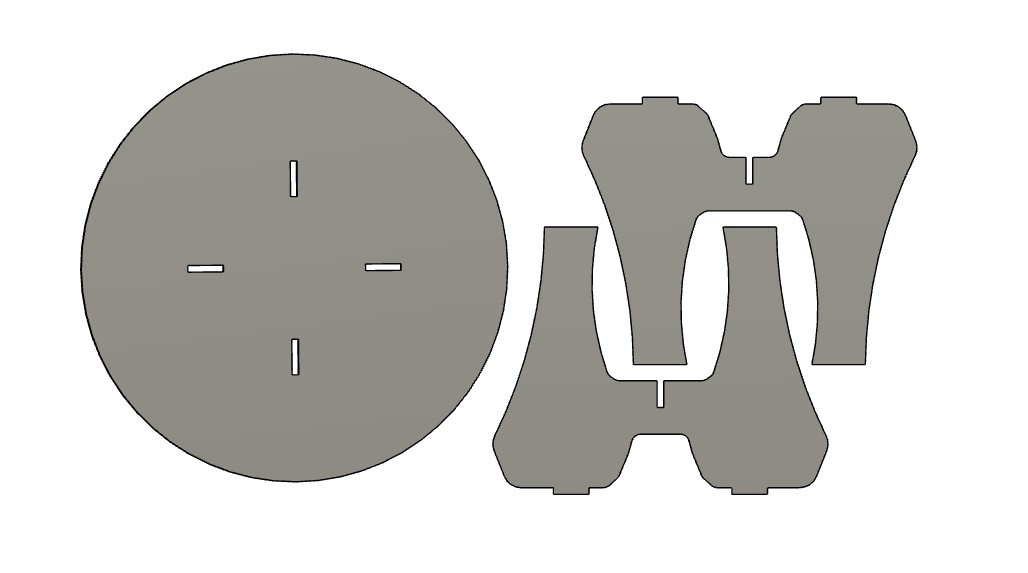 ## Cardboard test #2 Drawing set to cut  Quick cut on laser  And I think we are ready to cut ...now we just need the wood glue up  ## Wood glue up Chatting with Dr. Taylor about the table he had a great suggestion of using a glue up of hardwood to take the table to the next level. This was a great opportunity to learn 2 new things: 1. How to glue up hardwood panels 2. How to use the [Festool DOMINO Joiner](https://www.festoolusa.com/products/domino-joining-system/domino-joining-machines/576423---df-500-q-set-us) our lab has. 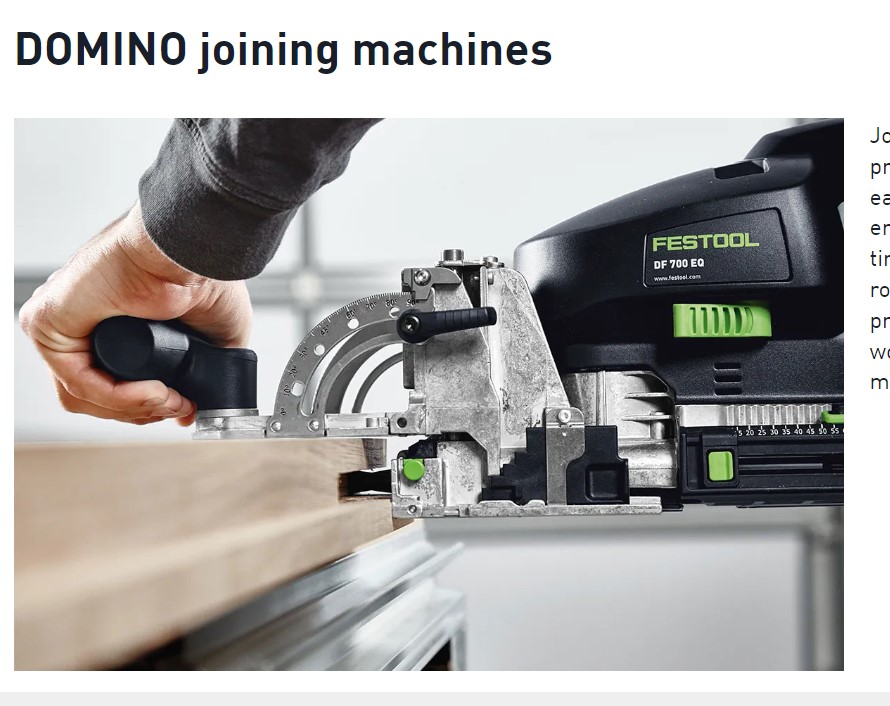{: style="height:300px;width:300px"} I headed out and got some nice wood planks 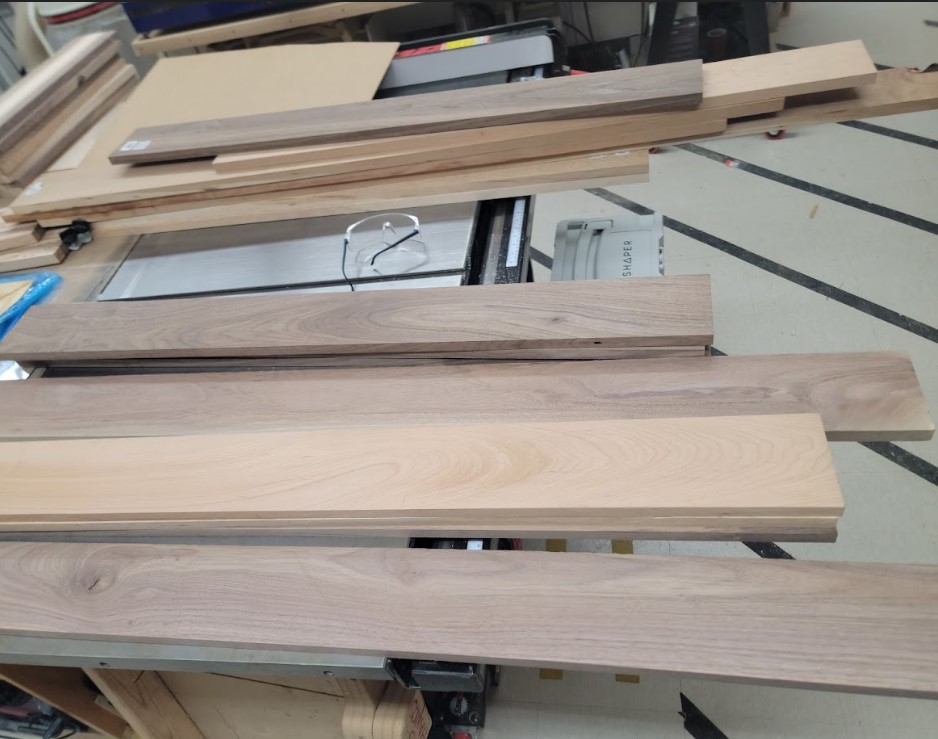 Next was the joiner to make sure the side were nice and flat 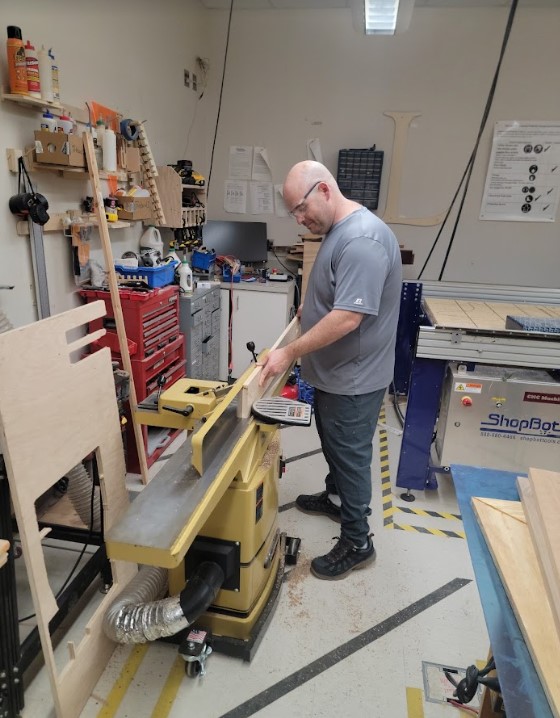 Next OI lined up all the planked to get the patters  I marked the planked every 8 inches for each place I will put a domino/dowel 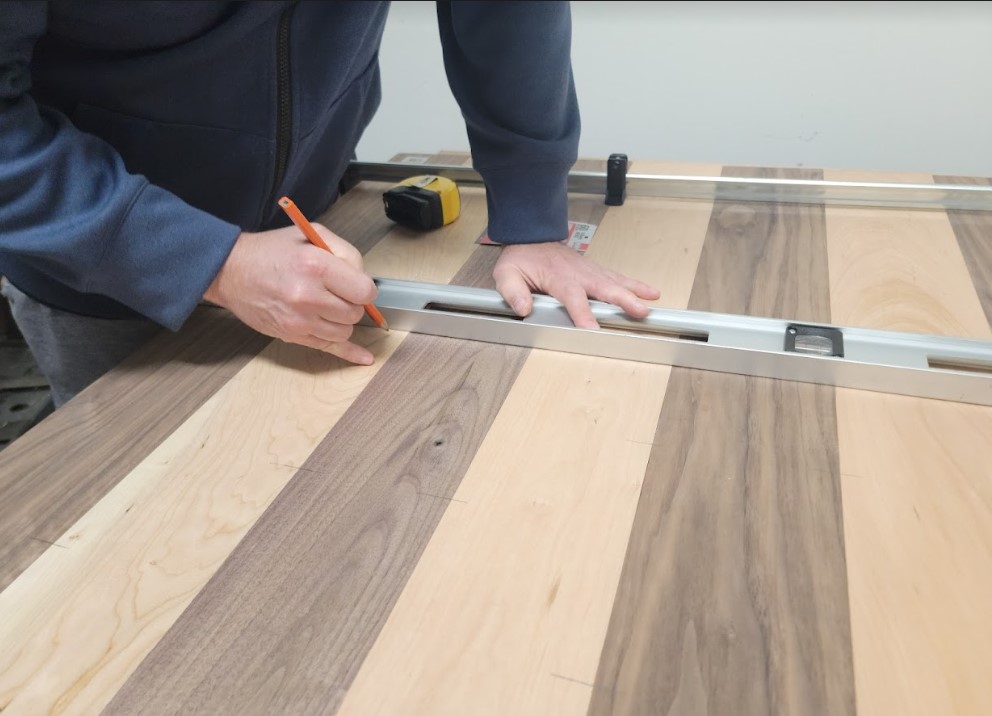 Next step was the drill holes at every marking for the dominos/dowels 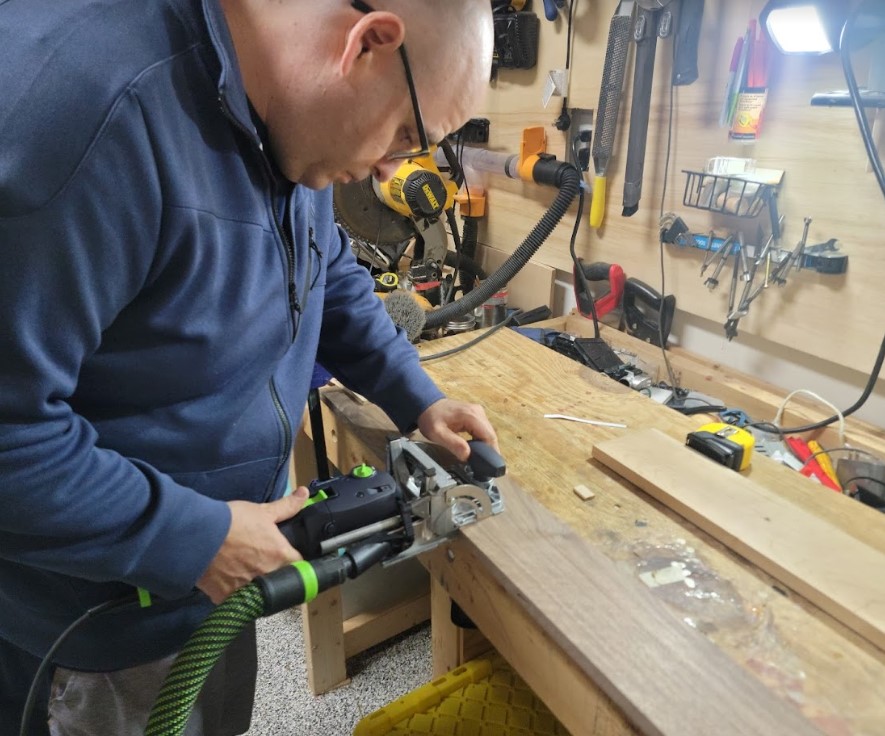 Here you can see the holes 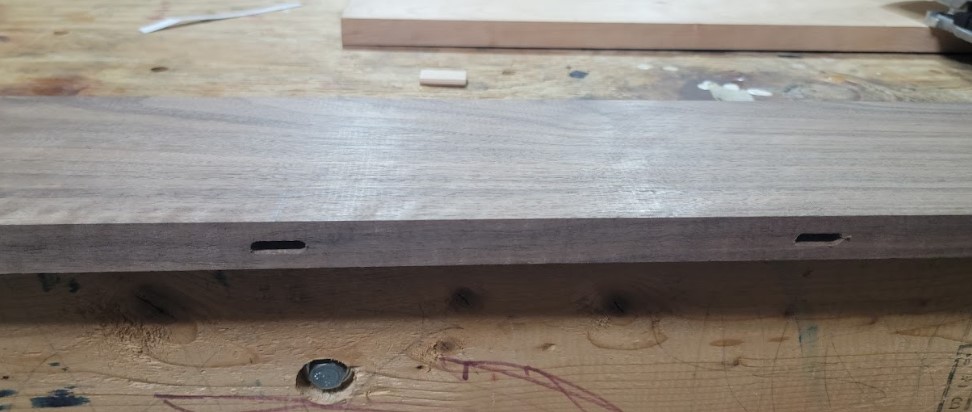 Now I set up each plank put glue and inserted dominos/dowels 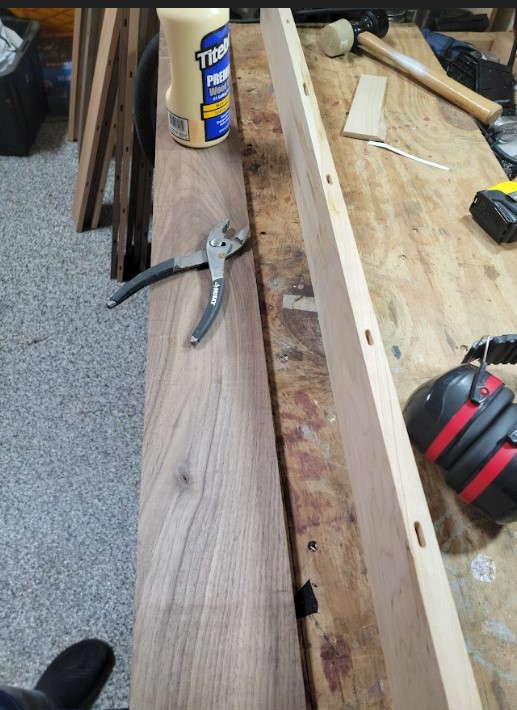 You can see how the line up 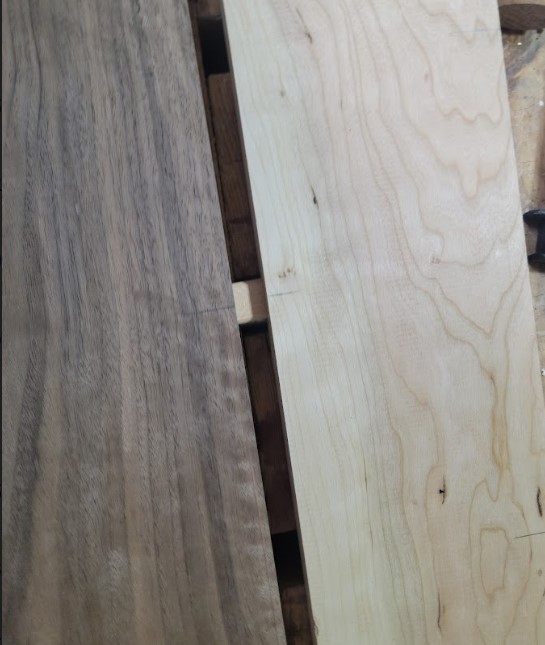 Now started to run through putting in wafter and then inserting next plank and stacking them together. I found out that it is very important to have the dowels all the way in to ensure a smooth stacking and so you can see I use a maleate to ensure all the dowel are in and then again to put in the next plank 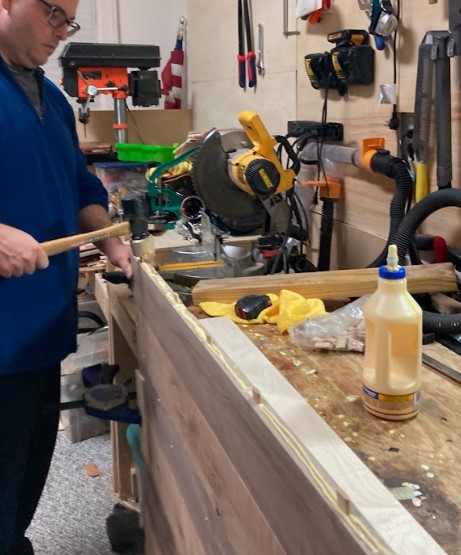 My dad who is 86 was visiting and come into the shop to supervise as I was working. He introduced me to woodworking when I was a childe and while his arthritis does not allow him to do any woodworking we had a good time working together. 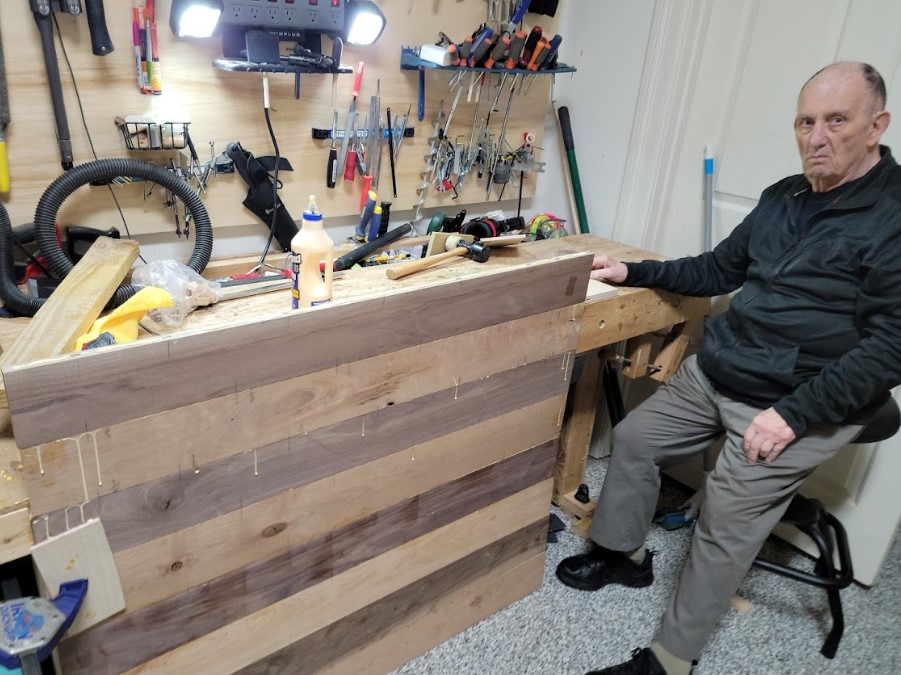 Next I moved to the glues panel to a flat surface and I use 4 long clamps to hold the planks together in addition I use 2 metal bars and smaller clamps on each edge to keep the panel from bowing as much as possible. 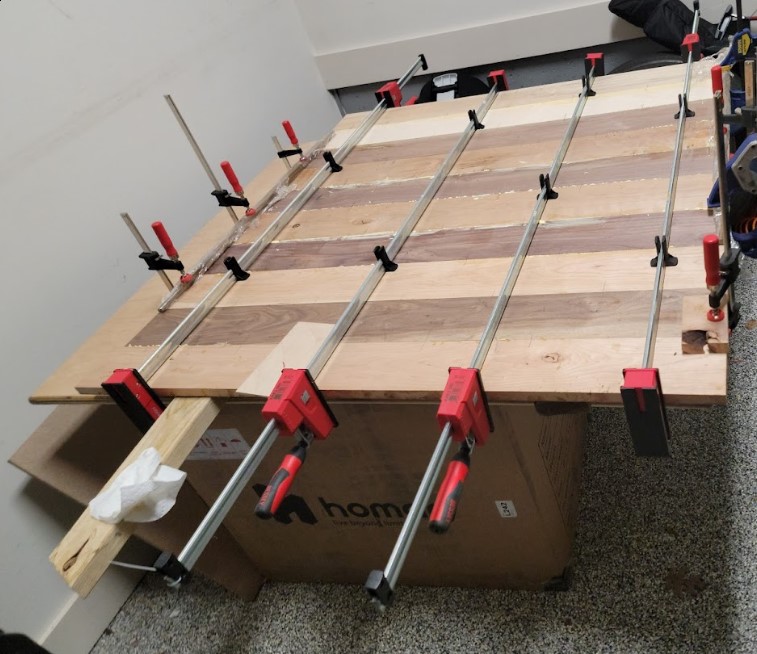 Another inspection approved 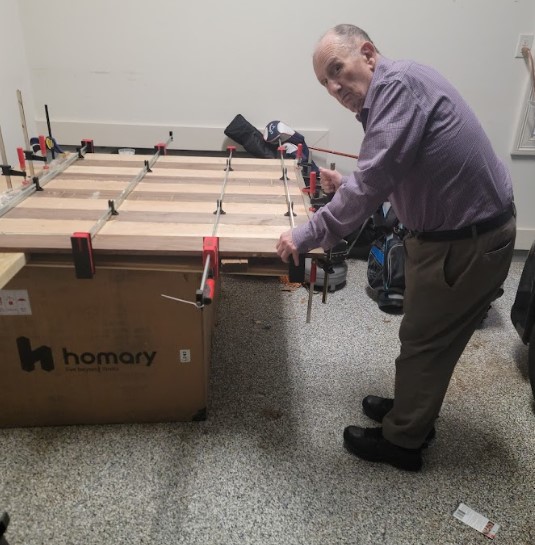 24 hours later the board was dry enough and loaded into my truck to free up the space to work on the next panel for the legs 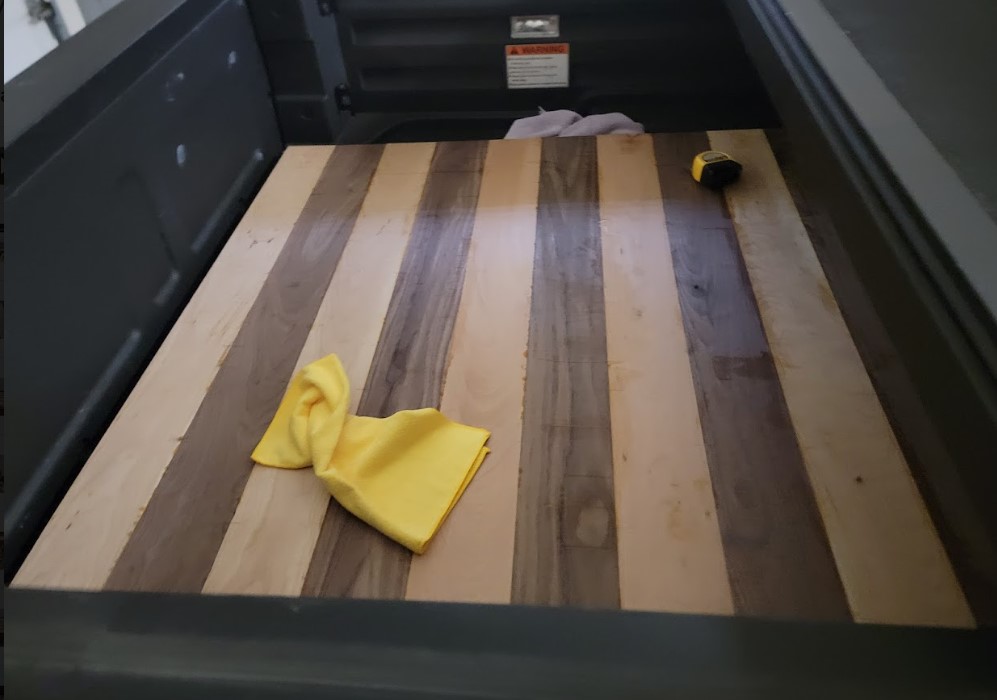 I repeated all the steps above and now panel #2 is drying 